Over the years, Lifetime’s products have continued to grow more complex. With a focus on innovation and continuous improvement, the manufacturer recognized the need to digitize and standardize its engineering and manufacturing workstreams. Paper-based processes and outdated systems weren’t able to keep up with the company’s growth. That’s when Lifetime turned to PTC to bring value across the organization.
Since its humble beginnings in a garage, Lifetime Products have come a long way
Headquartered in Clearfield, Utah and with more than 30 years of manufacturing experience, Lifetime owns and operates factories in Utah, Tennessee and China, as well as distribution centers in Ohio, Missouri, and Mexico. Lifetime currently sells goods in over 100 countries worldwide. The products it manufactures range from folding chairs and picnic tables to home basketball equipment and kayaks. Lifetime also produces OEM steel and plastic items for other companies.
Today, Lifetime is the world leader on both residential basketball equipment and polyethylene tables and chairs.
With mounting critical issues, a new approach to PLM was needed to continue growing profitably while producing quality products
For Lifetime, the journey to digital innovation started in 2005. The manufacturer was growing rapidly, which generated large amounts of new product data and designs. This became a challenge quickly. Both old and new drawings and product data were stored in 3-ring binders in the IT and R&D departments. Similarly, change management was paper based, with documents either sitting hidden in filing cabinets or worse, proliferating throughout the company ungoverned.
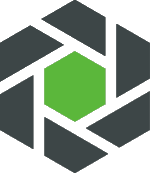
Go from 16 product related databases to one
Go from 45+ person meetings to an electronic change management system
Enable 400+ PLM users standardized globally
A half-measure to digitalization was insufficient. Whenever graphics, labels, or stickers were in a digital format, they were stored in personal hard drives. Engineering couldn’t get to those without calling somebody. Other departments such as Production, Manufacturing, Receiving, and Quality also needed product information and files, but locating and retrieving them was never easy. In total Lifetime Products relied on sixteen different data bases that stored all their product data.
Retrieving necessary data required memorization of product numbers and database locations. As a result, product development teams often found themselves spending more time managing and searching for data than designing innovative products. At the height of this data chaos, relatively simple engineering changes could end up requiring 45+ person meetings if enough product lines were affected.
Continuing down this path was untenable for Lifetime. When leadership realized that they had to improve their processes to keep up with their products, “they turned to PTC’s Windchill.
“Let’s be as innovative with our processes as we are with our products”
From 3-ring binders to digital BOMs, Lifetime leverages Windchill
1. CAD Data Management
As Lifetime’s product portfolio grew, it became clear that limited availability of drawings, graphics, and other product data was making collaboration increasingly difficult. Poor data management resulted in siloed engineering, manufacturing, and quality processes that were negatively impacting product development and inhibiting growth. The issues were numerous: engineering data was not available outside engineering, aside from hard copy drawings stored in binders, to get a drawing, employees had to physically locate the document (in some cases driving across the company campus), and then photocopy the file. As a result, engineering time was consumed by file management instead of product innovation.
Lifetime realized that in order to maintain continued success they needed to connect their product data so it could be easily shared across the enterprise. To that end, the first step in Lifetime’s digital transformation journey was to digitize their CAD data management. With Windchill, Lifetime enabled enterprise collaboration across design environments with a secure product data management system.
This new solution allowed stakeholders to go from hundreds of directories to a single data base for product data. It empowered internal and external teams to collaborate around product updates in real time. Critically, engineering could now implement revision control on CAD data and release procedures, including electronic sign off, and be confident that those changes propagated to downstream stakeholders.
2. New Product Introduction (NPI) and Change Management
Having organized their product data, Lifetime set out to improve their NPI and change management processes. At this point, both relied heavily on the engineering department for project management and execution. Their workflows did little to facilitate participation from downstream product stakeholders.
Furthermore, without standard workflows that could leverage the now organized and consumable product data, Lifetime was still operating in much the same way as when their product data was paper-based. This was too slow, labor intensive, and created opportunities for quality risks and missed milestones. As a result, the enterprise was not engaged with the product development cycle. Even for the ISO certification, Lifetime depended on five project managers who followed five different processes instead of one standardized approach.
To address these challenges Lifetime utilized standardized templates in Windchill for NPI project workflows, engineering change orders, and program management. With Windchill’s Change Management solution, Lifetime standardized its change management processes with automated out-of-the-box workflows tailored to its needs.
In doing so, leadership was able to deliver change coordination, access, and visibility. In addition, changes could now be associated directly to the affected data and could be executed enterprise- wide in real time instead of waiting weeks to be implemented.
3. EBOM, MBOM, and ERP Integration
At this point, Lifetime’s digital transformation was gaining traction. Most of the organization had started to see the benefits of a controlled standardized PLM system. However, their engineering bills-of-material (eBOMs) were still being delivered to a configuration management department, either via email or Excel spreadsheets, and this was an ongoing source of issues. Without integrated eBOM management, duplicate BOM information was still manually entered into their ERP systems. Similarly, manufacturing bills-of-material (mBOM) had to be created and updated by hand anytime a change to the design occurred. This was a recipe for poor quality and non-conformance, as stakeholders could easily make mistakes when transcribing updates or entirely neglect to make them.
A part-centric BOM approach was necessary to alleviate these risks. Lifetime upgraded their PLM capabilities and enabled the organization to leverage industry standard BOM best-practices and workflows. Teams could now collaborate around up-to-date product data, taking advantage of a “closed-loop” lifecycle system to comprehensively manage product configurations and derivative documents both upstream and downstream.
Leveraging Windchill’s robust BOM management capabilities, Lifetime established automated eBOM to mBOM transformations to improve component management. Visualizations and digital models also became available for use throughout the product development process. In addition, Windchill’s ERP integration capabilities improved efficiency and product data quality for Lifetime by eliminating the error-prone data duplication processes and instead automatically pushed BOM updates in Windchill to their ERP system. With that, Windchill became Lifetime’s single source for product data.
4. Parts Classification
As Lifetime’s products matured and product
lines grew, so did the parts and finished goods they were managing. At the beginning, Lifetime believed that creating smart part numbers – whereby the part number contains descriptive details and information – was a great solution. That was before they had access to powerful PLM tools to manage their data. Having adopted Windchill and implemented the other changes above, it was decided that smart part numbers were no longer needed. In fact, their continued use posed major problems. Smart numbering made it difficult to search for products and components, to the point where engineers found it easier to create entirely new parts than to find an established part for the same function. From a strategic perspective smart part numbers weren’t scalable enough for the company and required detailed training to be effective.
In preparing for this project, Lifetime conducted a study. As a sample test, a product design engineer was asked to compare the rivets used in five different products and found that across those five products there were five different rivets from three different suppliers. Further investigation identified a great deal of similar parts that could be used interchangeably suggesting an enormous amount of time and resources were being wasted on redundant design work and purchasing.
Better reuse required better parts classification and search functionality. Using Windchill parts classification, Lifetime implemented a part naming standard across the organization. They eliminated entirely their smart part number scheme and instead used requirements and classification attributes including functional characteristics, geometries, and specifications to organize and search for parts. This has helped accelerate design cycles by leveraging proven IP, reduced procurement costs by increasing purchasing volumes and decreasing inventory, and improved supplier quality by limiting the number of suppliers and parts that need to be managed.
The Impact: Lifetime is now enjoying the value of PLM
PLM is an enterprise tool. It is not [just] an R&D tool. PLM is a highly valuable tool that can make your whole organization much more efficient.”
With out-of-the-box functionality, seamless collaboration, and dynamic data visualization, Windchill enabled Lifetime to realize value quickly. The manufacturer was able to:
-
Go from 16 product related databases to one, which is Windchill
-
Go from 45+ person meetings to an electronic change management system
-
Enable 400+ PLM users standardized globally
-
Enable 50+ CAD users
-
Enable enterprise collaboration across 15+ teams
In addition, Lifetime Products has also experienced:
- Change management efficiency • Earlier planning cycles
- Enterprise integration
- Faster time to market
- Improved quality
- Increased focus on process
- Scalability
- Less design rework
- More time for innovation
- New growth capabilities
- New product improvements
- Project management efficiency
- Reduced waste, scrap, and rework
- Real time virtual access to data
See how other leading manufacturers are embracing digital transformation. Visit this case study on PTC.com
Get a no-obligation initial assessment
Whether you’re trying to solve technical problems, implement new technology tools and strategies, or improve efficiency, SPK and Associates can be a key part of your strategy. We can provide a free, no-obligation initial assessment on almost any technology or engineering situation. Contact us today at (888) 310-4540 or info@spkaa.com.