All medical device manufacturers understand that precision, safety, and regulatory compliance are vital in their industry. Without these precautions, individuals could be harmed. These strict requirements and extended life cycles often make the time between designing and manufacturing nearly ten times longer than consumer devices. To overcome this challenge, companies must adopt advanced tools such as PTC’s premier CAD solution, Creo. Creo provides a comprehensive solution to help medical device manufacturers design and produce devices that meet rigorous standards. From concept design to manufacturing, Creo ensures that medical devices are innovative yet safe.
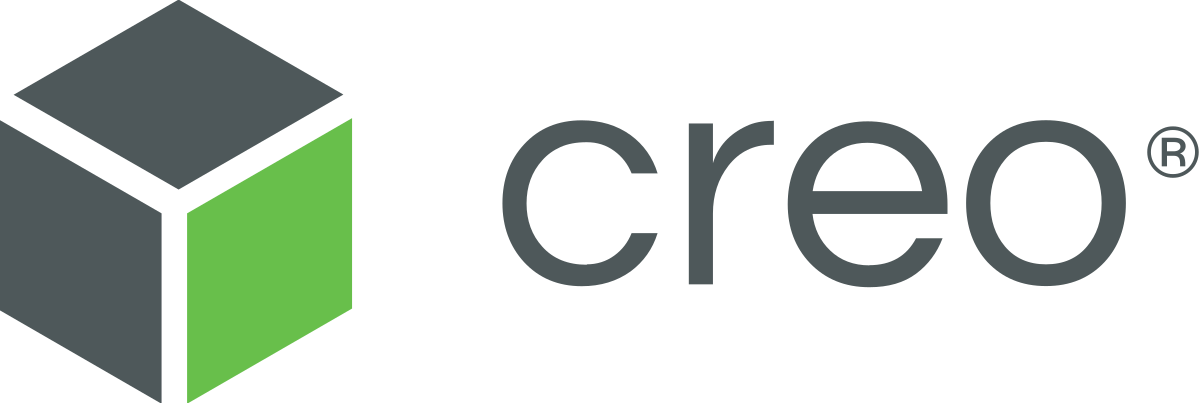
Overcoming Challenges in the Medical Device Industry with Creo
The first step to developing a medical device that meets industry standards is devising a well-planned product design. Engineers must balance usability, ergonomics, and functionality to create a successful product. There are a few key challenges within this process. For example, many tools need proper thermal management to ensure the temperature of the system ensures optimal performance and safety. Creo’s thermal management tools allow engineers to design devices that meet strict safety standards when in contact with a patient’s skin. Another key challenge is material selection. Creo’s material selection capabilities ensure the use of non-allergenic, durable materials capable of withstanding continuous cleaning and chemical exposure. By integrating these considerations into the design phase, companies can reduce the risk of failure, meet regulatory requirements, and improve product innovation and quality.
Concept Design Features
Creating a successful product is simple with Creo’s powerful design tools. As we have mentioned, Creo offers thermal management and material selection, however it also has features such as freestyle design and interactive surface design. These features enable the rapid creation of high-quality, stylized geometry that can be tailored to a device’s operational needs. Additionally, Creo enables engineers to create compact, portable devices with integrated sensors to meet the demand for smaller, multifunctional equipment. Furthermore, Creo’s AR design share improves collaboration to ensure all stakeholders are aligned on the device’s design, usability, and compliance requirements before moving on to the next step.
Refining the Medical Device Design for Compliance and Precision
As concepts evolve into detailed designs, Creo provides tools to refine every component for safety, durability, and manufacturability. Its behavioral modeling and generative design capabilities help optimize designs to achieve design goals and objectives. Furthermore, Creo helps mitigate risks associated with electrical hazards by allowing engineers to analyze and optimize designs for watertight protection against leakage. Features like GD&T Advisor ensure dimensional precision and compliance with industry standards, while advanced assembly capabilities streamline the integration of electrical components, mechanical parts, and protective housings. On top of all this, engineers can validate designs in real-time using simulation tools that assess structural integrity, thermal performance, and motion dynamics. These capabilities are critical for ensuring devices are visually appealing, robust, and able to sustain long service lives. Creo’s comprehensive approach minimizes potential hazards for patients.
Ensuring Quality and Compliance with Creo’s Simulation Capabilities
Simulation plays a pivotal role in the development of safe, reliable, and high-performing medical devices. Creo’s robust simulation capabilities enable engineers to validate and optimize designs early in the process, reducing the need for costly late-stage corrections. One of Creo’s standout features is Creo Simulation Live, which provides real-time feedback during the design process. Engineers can use it to evaluate how the device reacts under a range of conditions. For instance, designers can simulate heat distribution to ensure devices remain safe during prolonged contact with patients or optimize structural elements to withstand continuous use and rigorous cleaning protocols.
Advanced simulation tools, such as Creo Ansys Simulation, test specialized conditions. Its capabilities such as injection molding analysis and clearance and creepage analysis, enable engineers to refine designs for manufacturability and electrical safety. These tools help ensure that designs comply with strict medical device regulations, such as watertight protection against leakage and protection against electrical hazards. For highly dynamic applications, Creo’s mechanism dynamics features allow engineers to analyze and optimize moving parts within a device, ensuring smooth operation. By incorporating simulation at every stage of the design process, Creo empowers medical device manufacturers to make data-driven decisions. This not only eliminates design flaws but brings high-quality, compliant devices to market.
Manufacturing: Seamlessly Meeting Regulatory Standards
Creo’s capabilities extend seamlessly from design to manufacturing. Its high-speed NC machining solutions, additive manufacturing tools, and automated mold design streamline production processes. Medical devices often require precise plastic components that endure intensive cleaning and rigorous use. Creo’s tooling design and injection molding capabilities address these requirements, enabling the production of durable, visually appealing products. Additionally, its solutions ensure that devices are easy to clean without leaving residue, meeting both usability and safety standards. Furthermore, Creo’s integrated simulation and manufacturing tools ensure that devices meet quality and performance standards throughout their life cycles. This is highly important for medical devices as they have an extended service life compared to other consumer products. Overall Creo’s features reduce costs and improve efficiency for the design and manufacturing process.
Ready to Use Creo for Medical Device Manufacturing?
The best medical devices prioritize precision, safety, and compliance. Creo equips companies with an end-to-end solution allowing them to easily create the highest quality products. If you would like to discover how you can achieve excellence in medical device engineering with Creo, contact us today. Let’s create the future of healthcare together!