PLM solutions like PTC Windchill help organizations manage every facet of the product lifecycle. One of the best features for organizing these components is a Bill of Materials (BOM). Many PLM solutions integrate BOM management because it facilitates collaboration amongst shareholders. Organizations that utilize a BOM continuously remain organized during the PLM process.
What is a BOM?
A BOM is a list of all the required components for manufacturing a product. It is a detailed document utilized by all employees to ensure consistent, accurate manufacturing operations. In the past, BOMs were hand-written, which did not enable collaboration. With today’s technology, organizations can have a digital BOM that implements a part-centric approach. This approach utilizes the BOM as a database for all defining product information. The BOM then accesses additional product data. This data can include other BOMS, documents, drawings, or specifications. The part-centric approach creates one definition to come back to while storing all other information alongside it.
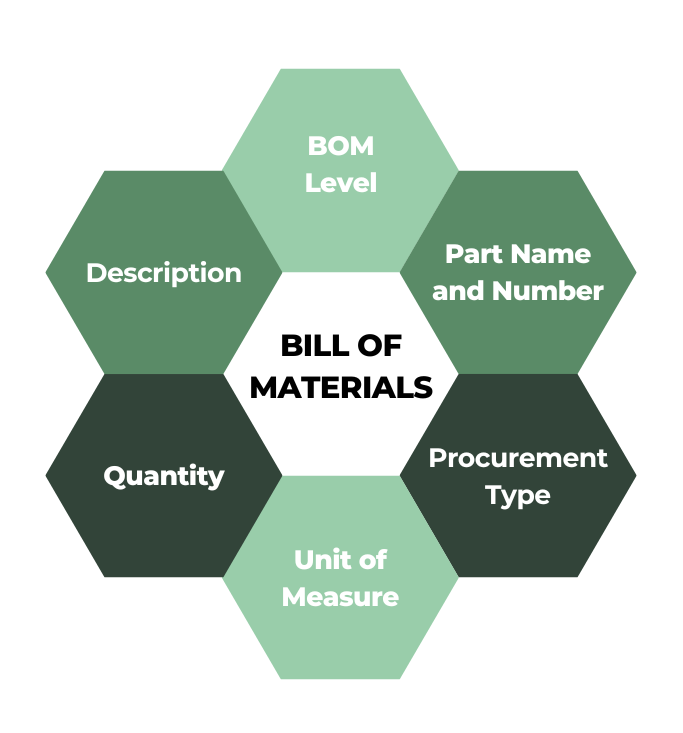
What Can a Part-Centric BOM Do?
A part-centric BOM is used as a reference point for all stakeholders. This cross-discipline visibility aims to reduce confusion for users and eliminate errors. Part-centric BOMs enable users to automate change processes and successfully communicate these changes. Additionally, users can define product families and easily filter the product structure to find specific information. Furthermore, BOMs work well alongside configuration management properties. Once users configure a product, they can generate a variant. This variant eliminates redundancies, making them reusable.
Written vs Digital BOM
Conversely, a written product definition risks confusion along the product line and is not adaptable. There are too many parts of the product lifecycle for BOM management systems to manage just one structure. That is why the part-centric approach works so well. When the Engineering Bill of Materials (eBOM) is altered, all the derivatives update alongside it. The eBOM can also be used for different purposes if needed. This includes the Software Bill of Materials (sBOM) or Manufacturing Bill of Materials (mBOM).
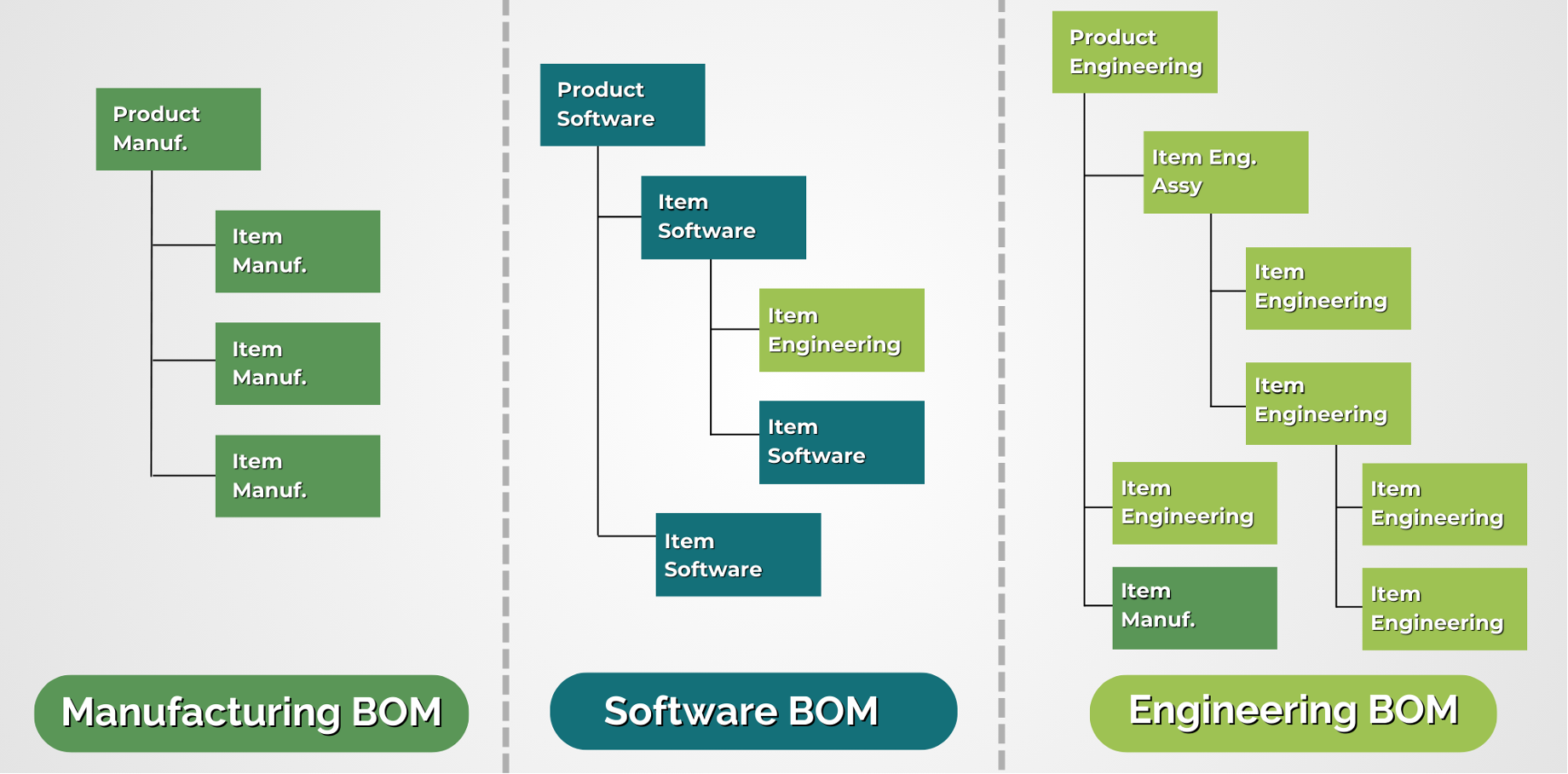
Problems Part-Centric BOMs Resolve
There are many advantages to implementing a part-centric BOM in your PLM processes. Let’s explore some common issues and how the BOM resolves them.
- Slow Time-To-Market: BOMs help get products to market faster by eliminating quality issues.
- Efficiency Issues: Automated BOMs display correct information, eliminating confusion and increasing efficiency.
- Miscommunication: All stakeholders can view product changes in the BOM without speaking with anyone. They are consistently informed.
- High Product Costs: BOMs help reduce administrative costs associated with supply chain management and consolidate like-parts to leverage purchasing power.
- High Workloads: Consolidating like-parts lessens the workload for overworked stakeholders.
- Poor Resource Allocation: When a part-centric BOM is combined with project management tools it’s easy to spot roadblocks and reallocate resources to operate efficiently within a budget.
- Inefficient Portfolio Management: A digital BOM allows users to identify portfolio characteristics and create changes.
Ready to Implement a Part-Centric BOM?
A part-centric PLM approach resolves many issues in the PLM process and leads to more efficient business results. This has been continuously proven by Windchill PLM users for over 30 years. If you would like to learn more about BOM management or Windchill PLM, or want to implement a part-centric BOM approach for your business, contact one of our experts today.