Ensuring regulatory compliance and fostering trust in products are paramount for medical device manufacturers. The FDA, European Competent Authority, and Health Canada closely oversee design, development, and manufacturing for patient safety and efficacy. Fundamentally, adhering to best practices facilitates market access, enhances operational efficiency, reduces time-to-market, and mitigates legal liabilities. In this guide, we’ll explain design controls best practices and more.
Design Controls Are The Foundation of Compliance
In an industry where innovation saves lives, embracing best practices is not just a regulatory requirement but a moral obligation to patients and healthcare providers worldwide. Design controls best practices serve as a foundation for demonstrating compliance with regulatory requirements. These are a few of the initial key factors to consider when establishing design control practices:
- Establishing a cross-functional team comprising experts from design, engineering, quality assurance, regulatory affairs, and manufacturing ensures a holistic approach to design controls.
- Clear documentation of design inputs, including user needs, intended use, and regulatory requirements, lays the groundwork for the entire design process.
- Incorporating risk management, following ISO 14971, is vital for identifying and mitigating potential risks in medical device design. Learn more about tools for ISO 14791.
- Iterative design reviews at crucial milestones enable early issue detection, ensuring the final design aligns with all requirements.
- Validation and verification processes ensure the designed outputs align with inputs, and the device functions as intended.
Now we’ve covered the high-level considerations, let’s take a deeper look at medical device design control best practices.
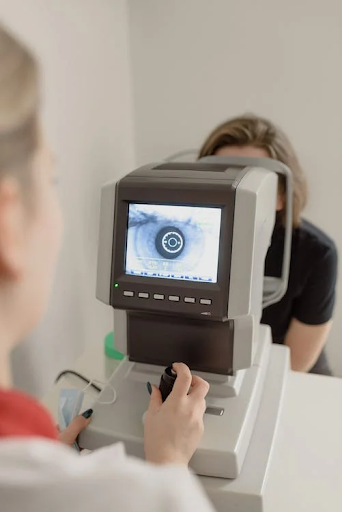
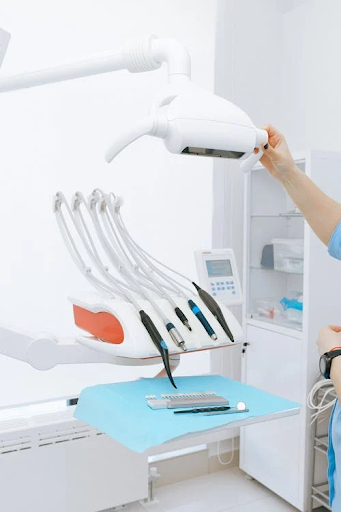
EQMS Design Control Best Practices
The utilization of an Electronic Quality Management System (EQMS) is paramount in enhancing design control practices in the medical device industry. Additionally, it also plays a crucial role in the management of the Design History File (DHF). Essentially, by providing a centralized repository and facilitating version control, EQMS ensures all design-related documents, including those crucial to the DHF, are systematically managed and accessible. This includes records of design inputs, outputs, verification and validation activities, design changes, risk management documentation, and design reviews, all seamlessly integrated into the EQMS. This comprehensive approach not only aligns with design control best practices but also ensures the DHF is effectively compiled and maintained, meeting regulatory standards and contributing to the overall success of medical device development.
Furthermore:
- Workflow automation aligns with the sequential nature of design controls, optimizing processes and minimizing errors.
- Cross-functional collaboration is promoted through shared platforms, fostering communication among design, engineering, quality assurance, and regulatory teams.
- Real-time visibility and detailed audit trails support transparency and compliance during audits, crucial aspects of design controls.
- Integration with risk management modules ensures that potential risks are considered throughout the design control process, as mandated by ISO 14971 standards.
Additionally, a good eQMS like Greenlight Guru or the eQMS module in MasterControl provides training management modules to ensure personnel involved in design control activities are appropriately trained.
At SPK, we highly recommend utilizing an eQMS like Greenlight Guru that is specifically developed for medical device manufacturers. You can also check out this guide to ensure a successful, integrated eQMS implementation.
Risk Management Design Controls
Aligning with ISO 14971 standards, integrating risk management into medical device development proactively identifies and mitigates potential risks. The objectives of design controls and risk management closely align. Both aim to:
- Address user needs.
- Meet requirements.
- Adhere to standards.
- Ensure overall performance.
Thoroughly defining and documenting user needs, design inputs, outputs, verification, validation, and reviews are crucial to ensuring a medical device’s safety. Additionally, systematically assessing and addressing potential risks throughout the development process:
- Minimizes the likelihood of post-market issues.
- Safeguards patient safety.
- Contributes to the overall success and longevity of the medical device.
Ensuring Transparency and Accountability In Design Control Best Practice
Traceability matrices assist in highlighting the connections between diverse design elements and the corresponding regulatory requirements. This aligns with the principles outlined in ISO 13485:2016, mandating traceability to ensure transparency and effective tracking throughout the entire design process.
In line with design control best practices, integrating specialized software tailored for regulatory compliance becomes paramount. This technology not only expedites the time-to-market but also mitigates potential risks linked to the manual upkeep of traceability matrices. Through the application of specialized software, operational efficiency is heightened, and the risk of errors is minimized. This emphasis on technology-driven traceability significantly contributes to the creation of accurate and reliable documentation, serving as a fundamental element within the framework of design control best practices for the development of medical devices.
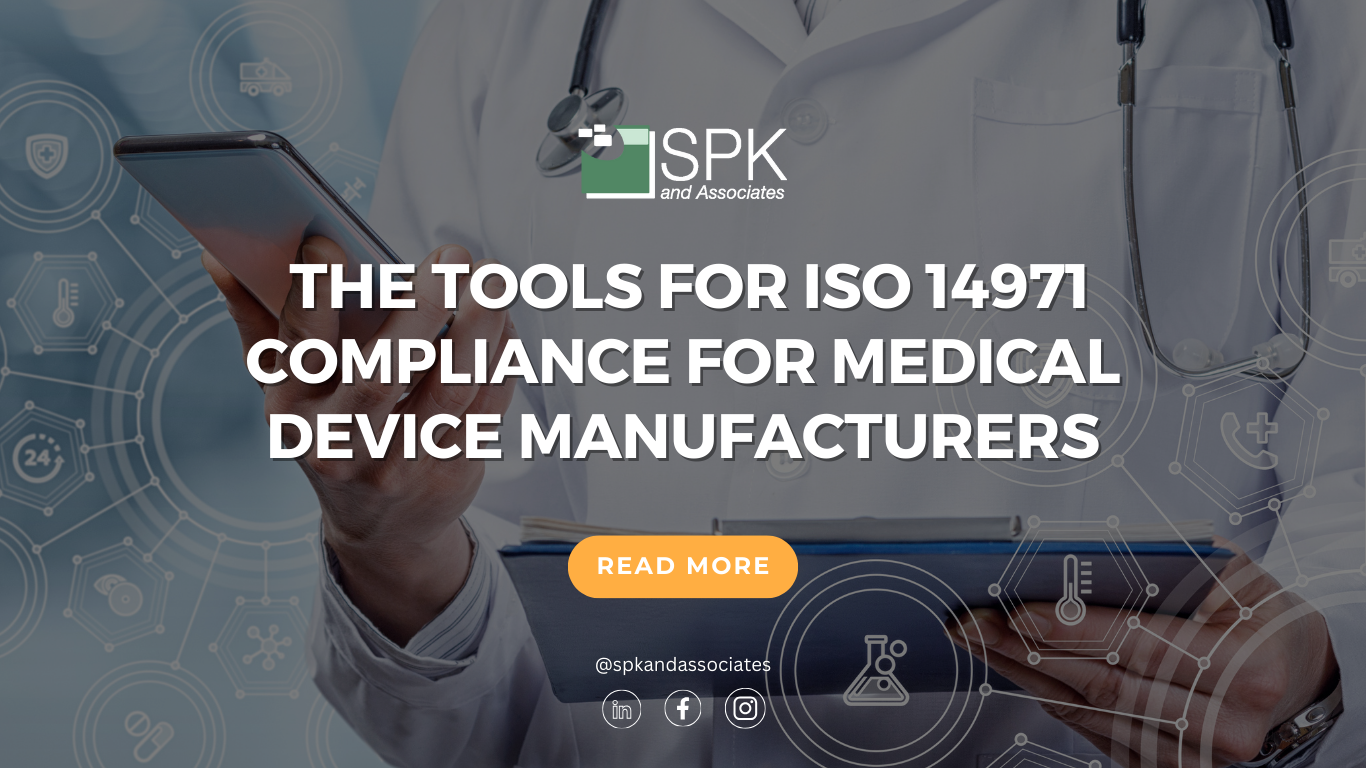
Design & Development Planning
Contrary to common belief, both FDA regulations and ISO 13485:2016 emphasize the importance of design and development planning in managing design activities. In fact, design reviews are necessary for evaluating and agreeing upon design controls throughout the medical device development process.
High-level steps towards design control excellence involve dynamic planning considering:
- The stages of design and development.
- Defining responsibilities.
- Establishing interfaces between different groups or activities.
In this dynamic planning phase, essential participants encompass diverse functions. For example engineering, marketing, and manufacturing with the inclusion of an independent resource to ensure an unbiased perspective.
Design reviews, conducted at critical junctures, provide a comprehensive evaluation of the design controls implemented throughout the development process. Essential elements include:
- Identification of Stages: Clearly define and identify the different stages of design and development. This includes conceptualization, prototyping, testing, and finalization.
- Responsibility Assignment: Clearly define and assign responsibilities at each stage. This ensures accountability and transparency in the design control process.
- Interface Establishment: Establish clear interfaces between different groups or activities involved in the design and development process. Effective communication and collaboration are essential for seamless integration of design controls.
- Inclusion of Independent Resource: Include an independent resource in design reviews to provide an unbiased perspective. This ensures that design controls are rigorously evaluated without internal biases.
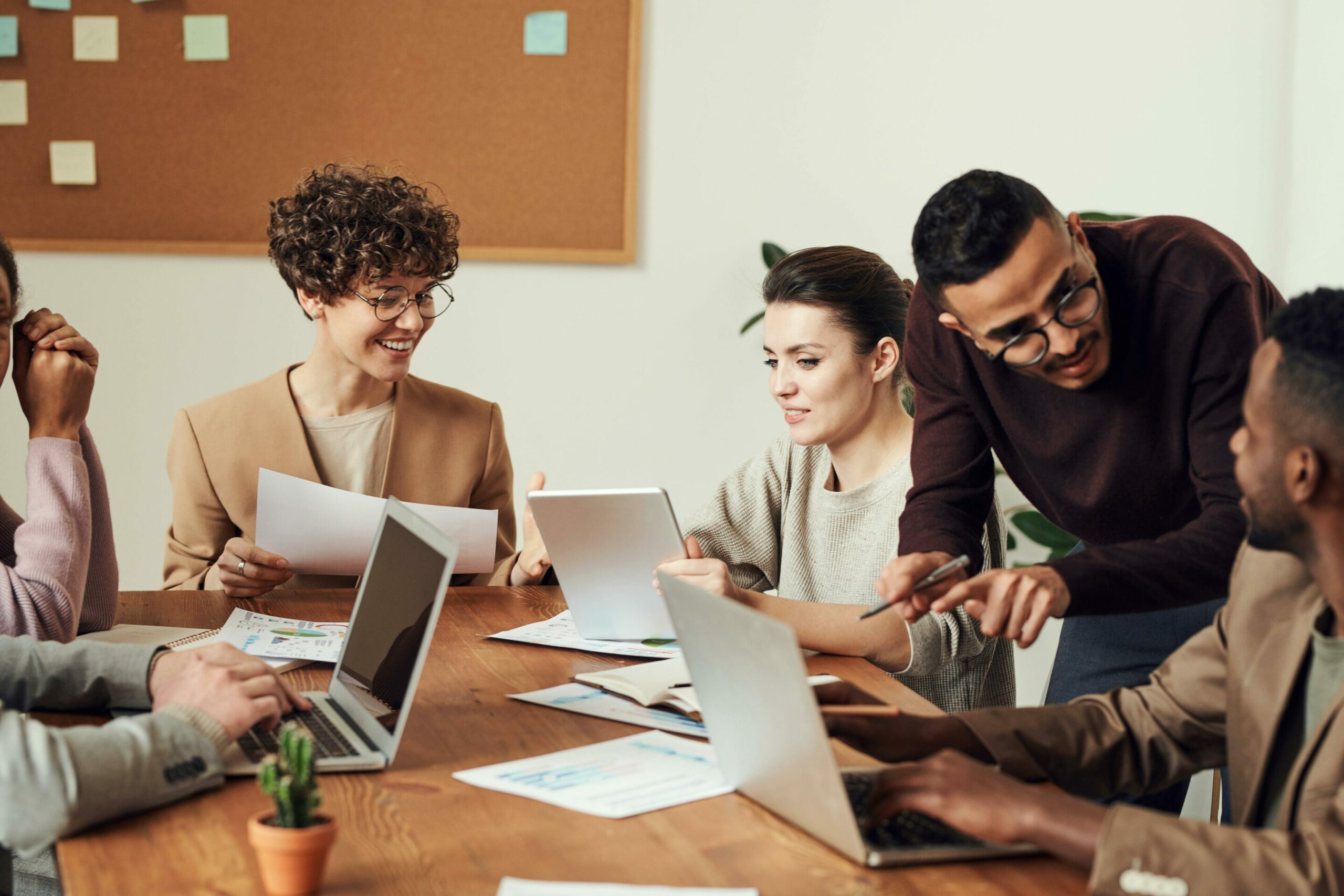
Embracing Best Practices for Excellence
Mastering design controls is not only essential for regulatory compliance but also paramount for manufacturing safe and effective medical devices. By integrating best practices in design controls, quality management systems, risk management, and traceability, manufacturers can navigate regulatory complexities with confidence.
At SPK and Associates, we are committed to guiding you on this journey towards excellence in design control and regulatory compliance. Our expertise and collaborative approach can ensure your medical devices meet the highest standards. Ultimately we’re focused on contributing to the well-being of patients and the success of your organization.
Contact us today to get the right support for your medical device development.